Sustainability is becoming a central focus in modern manufacturing, prompting significant changes across the machining industry. As industries seek to reduce environmental impact while maintaining high productivity, hole-making tools are undergoing a transformation in design, materials, and usage. In particular, the evolution of tools like the High Speed Steel Twist Drill and deep hole drilling tools illustrates how sustainability and performance can coexist in today’s competitive environment.
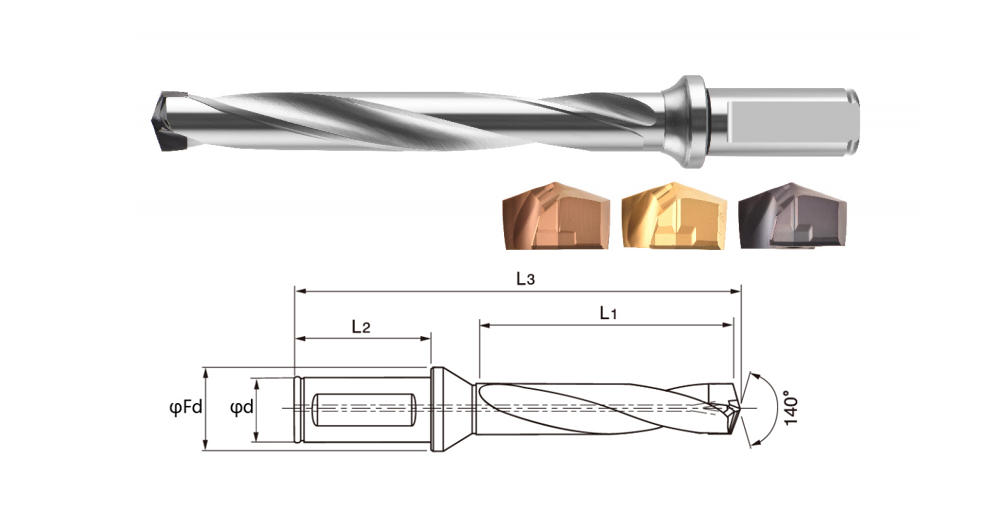
A growing number of manufacturers are revisiting traditional tool materials and coatings. The High Speed Steel Twist Drill, long valued for its balance of toughness and affordability, remains a relevant choice in many operations. However, newer versions are being engineered with sustainability in mind. Coatings with longer life spans and lower environmental footprints are becoming more common. This shift reduces the frequency of replacements, decreasing material waste and lowering overall consumption.
Similarly, deep hole drilling tools are being refined to less resource use while maintaining precise performance. These tools, essential in sectors like aerospace and automotive, require high levels of accuracy during prolonged use. As manufacturers focus more on efficiency, they are improving chip evacuation and cooling mechanisms. By enhancing these aspects, toolmakers can reduce the need for excessive cutting fluids, some of which can be environmentally hazardous.
Another emerging trend involves the reuse and refurbishment of worn tools. The High Speed Steel Twist Drill, in particular, is well-suited for regrinding, which extends its usability. This practice not only cuts down on raw material consumption but also lowers energy use during production. Tool management systems now often include strategies for tracking tool wear and scheduling refurbishments, encouraging a circular lifecycle rather than a disposable model.
In parallel, the development of advanced geometries in deep hole drilling tools supports better material removal rates with less input energy. New flute designs and point angles are helping these tools work more efficiently across various materials, from hardened steel to composite alloys. This increase in versatility supports flexible production lines, which are crucial in sustainable operations aiming to reduce changeover times and excess inventory.
Digital technologies are also contributing to more responsible tool usage. Real-time monitoring systems can now track the performance of each High Speed Steel Twist Drill used in machining centers. By analyzing data related to wear, vibration, and temperature, operators can make informed decisions that extend tool life and prevent premature failure. These systems, when applied to deep hole drilling tools, help avoid unnecessary replacements and support consistent quality, especially in critical applications.
Training and awareness among operators are essential to these advancements. As machining teams adopt new sustainable practices, they learn to handle the High Speed Steel Twist Drill with techniques that reduce tool stress and energy use. Similarly, knowing how to correctly apply deep hole drilling tools improves not only performance but also safety and waste reduction. A knowledgeable workforce plays a key role in making sustainability a daily priority.
The High Speed Steel Twist Drill will likely continue to evolve with new alloys and surface treatments, while deep hole drilling tools may incorporate even more precise controls and adaptive features. Together, these developments demonstrate how the machining industry is adapting to meet the demands of a sustainable future without compromising efficiency or precision.
Contact Us